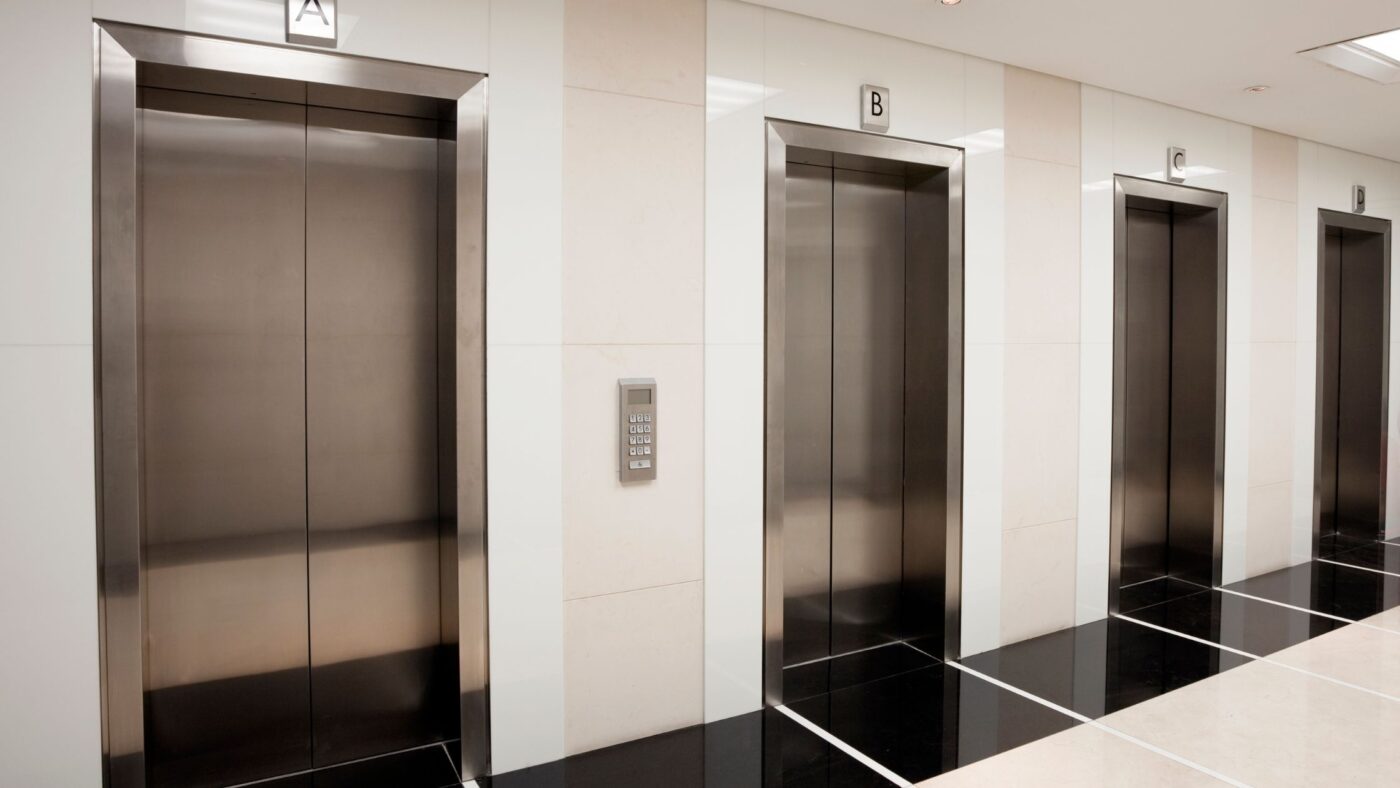
Have you considered the safety and performance of your home lift in Australia? Routine inspections help ensure your lift operates smoothly and meets Australian safety standards. Home lifts are often essential for ease of movement within multi-story homes, and inspections keep them reliable and secure.
A home lift inspection identifies any wear, addresses potential issues, and ensures all parts function as expected. This guide provides a detailed look at what happens during an inspection and offers clear insights to help you understand the process.
Understanding Home Lift Inspections
Residential lift inspections ensure that every part of the lift works safely and correctly. Inspectors start by visually checking the lift for any obvious issues like rust or loose parts. They then test all safety systems, including brakes and alarms, to ensure they work in emergencies. Next, mechanical parts like pulleys and belts are inspected for any need for repairs or adjustments, which are common for lifts exposed to high humidity in some Australian regions. Inspectors also check the controls and sensors to confirm the lift stops at the correct floors and responds accurately. Finally, they inspect the doors to ensure they open and close smoothly, without sticking. This full inspection helps keep the home lift safe and reliable for everyday use.
What to Expect During an Inspection
An inspection for a home lift generally includes the following steps:
Visual Inspection
- Inspectors start with a thorough visual assessment. This involves checking the lift’s exterior, interior, and visible components for signs of wear, rust, or damage. Any misalignment, dents, or wear in the framework or cables is noted. A visual check helps determine if further examination is necessary for specific parts.
Mechanical Inspection
- In this step, inspectors examine the core mechanical parts, such as pulleys, guide rails, and belts, which ensure the lift’s smooth and safe movement. Any wear or misalignment in these parts can affect the lift’s functionality. Inspectors may suggest elevator maintenance if they detect signs of wear or if parts need lubrication or adjustments.
Electrical Inspection
- The lift’s electrical system powers its movements and controls. Inspectors check wiring, connections, and circuits for any signs of wear, damage, or loose connections. They ensure that all electrical components function efficiently, minimizing risks of unexpected breakdowns.
Safety Device Testing
- Safety is the top priority. This part of the inspection includes testing emergency systems such as brakes, alarms, and sensors. Inspectors ensure these devices operate as expected, protecting in case of power failures or other issues. Proper testing of these devices ensures the lift’s compliance with safety standards.
Documentation
- After the inspection, inspectors record all findings in a detailed report. This documentation includes notes on the condition of each component, any issues identified, and recommendations for repair elevator services if necessary. This report helps homeowners keep track of the lift’s maintenance history and follow up on required actions.
Preparing for an Inspection
Getting your home lift ready for inspection involves a few simple steps. Each step helps the inspection go smoothly and ensures your lift stays in top condition.
- Cleaning the Lift: Start by cleaning the lift cabin and doors. Remove any dust, dirt, or spills. A clean lift makes it easier for inspectors to spot any issues. For instance, cleaning the buttons and panels allows them to test controls without any interference.
- Gathering Necessary Information: Have any recent repair records, maintenance logs, and service history ready. This gives inspectors a clear idea of the lift’s condition and any past issues. If, for example, a part was recently replaced, they’ll know to check if it’s working correctly.
- Providing Access: Ensure clear access to the lift and all related equipment. If the inspection requires access to the lift’s machinery or control panel, have those areas unlocked and clear of obstacles.

Benefits of Regular Inspections
Routine inspections offer multiple benefits, from safety to reliability. Here’s why they matter:
- Improved Safety: Regular inspections catch issues early, ensuring the lift is safe for daily use. For example, if a safety brake isn’t working as it should, an inspection will catch it before it becomes a problem.
- Increased Reliability: Inspections help avoid sudden breakdowns. By identifying worn-out parts, like cables or pulleys, in advance, you reduce unexpected downtime and keep the lift ready when needed.
- Extended Lift Lifespan: Regular check-ups keep the lift in good condition, extending its life. Like regular car maintenance, frequent inspections prevent wear and tear from building up over time.
- Compliance with Regulations: Inspections ensure your lift meets safety standards and regulations. For instance, a certified lift inspector will confirm your lift follows all legal safety requirements, which can be helpful for insurance and legal compliance.
Get Timely Elevator Maintenance with SWIFT Lifts
Keeping your home lift in top shape is easy with SWIFT. Maintenance happens just once or twice a year. When it’s time, a SWIFT technician will come to your door, check every part, and ensure everything meets high standards. Only genuine SWIFT parts are used for repairs, giving you years of safe, worry-free use.
With SWIFT’s “SWIFT Remote” system, you get fast support through wireless diagnostics that alert you if extra service is needed. Regular software updates mean your lift stays as smooth and safe as ever—and may even improve over time. Plus, our 24/7 support hotline is always available for you. For details on maintenance packages, click here.
FAQs
It’s generally recommended to have your home lift inspected at least once a year. However, if you use the lift frequently or notice any unusual sounds or movements, consider scheduling an inspection twice a year. Regular inspections help identify minor issues before they become costly repairs, ensuring safe and smooth operation for daily use.
During a home lift inspection, the technician will perform a series of checks on the lift’s core components. This includes safety testing for emergency brakes and alarms, examining mechanical parts like pulleys and belts, and inspecting the electrical systems to ensure everything is in working order. The technician will also assess the door functions, ensuring they open and close smoothly, and confirm that all control buttons and sensors respond accurately. These steps help maintain the lift’s reliability and performance.
A standard home lift inspection usually takes between 1 and 2 hours. The exact time may vary depending on the lift’s condition and any specific issues that need attention. For example, if the technician finds parts requiring extra testing or minor adjustments, the inspection may take a bit longer to ensure everything is fully operational.
Common issues identified during inspections can include worn-out cables, pulleys, or belts, which may cause uneven movement or noises. Electrical problems, such as loose wiring or malfunctioning sensors, can also be flagged for repair. Doors that don’t close fully or buttons that respond slowly may also be noted. Catching these issues early during a routine inspection helps prevent sudden breakdowns and keeps your lift running smoothly.
If the inspection highlights any issues, the technician will provide a detailed report outlining the necessary repairs or adjustments. It’s essential to address these promptly. SWIFT uses genuine parts to ensure repairs are reliable and long-lasting. Additionally, our “SWIFT Remote” system enables quick diagnostic support for immediate troubleshooting, and you can reach our 24/7 hotline for additional assistance at any time.
Get In Touch